Orthotropic - Projects
Orthotropic has been privileged to contribute to many exciting engineering projects since our establishment in 2018. We can’t talk about everything we’ve done, but please explore the links below to find out about some of our projects and customers…
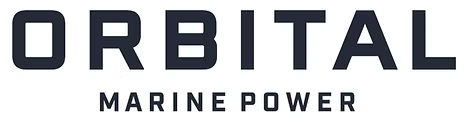
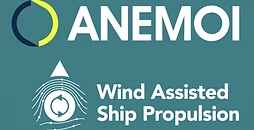
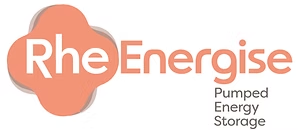
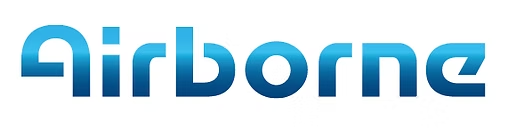
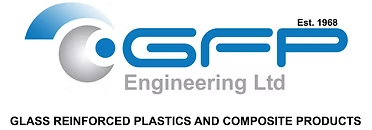
Access bridge design
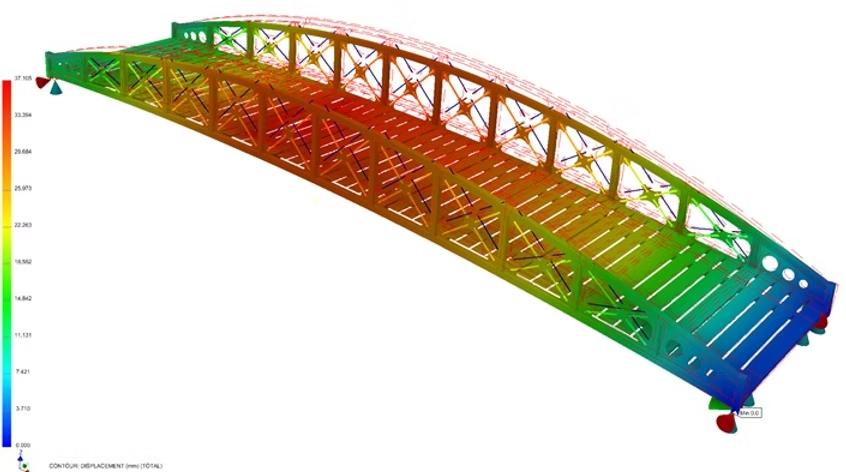
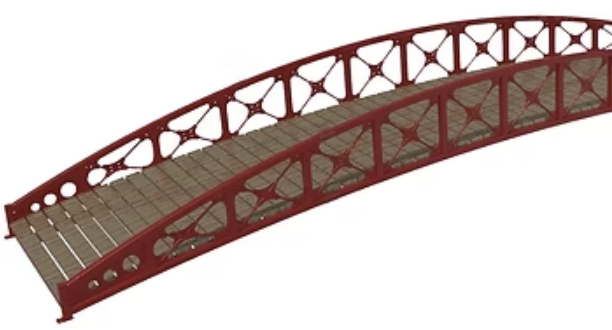
Our first end – to – end design project, completed in 2019! Orthotropic was commissioned to design a 14m steel and timber access bridge to handle routine light traffic as well as the occasional heavy vehicle. We completed the preliminary and detailed design work, CAD modelling and structural analysis, providing our client with a detailed design report and a comprehensive set of manufacturing drawings.
Tidal blade design support
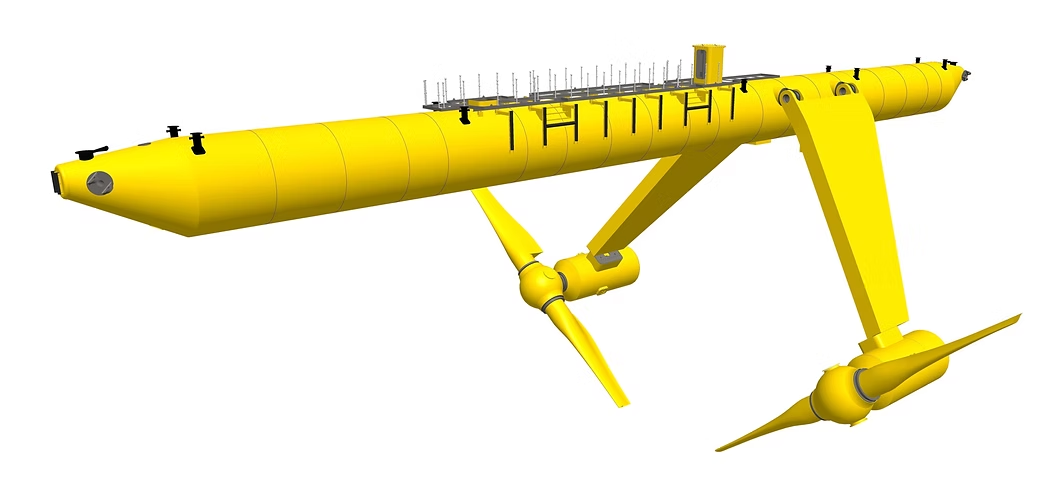
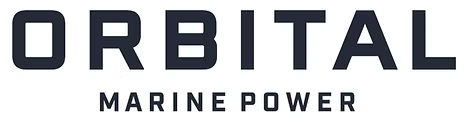
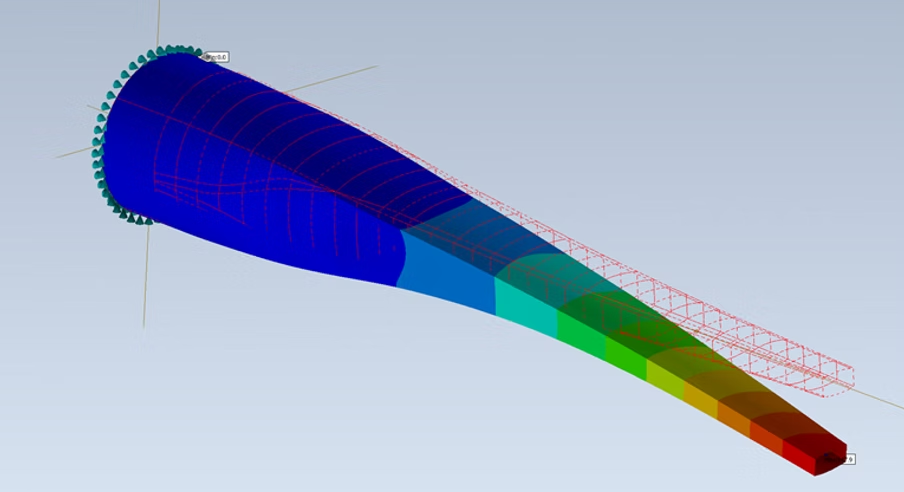
We were pleased to support Orbital Marine Power during the design of their O2 tidal turbine; at 2MW the world’s most powerful! Orthotropic undertook the preliminary design of the composite blade spar laminate, and conducted analyses of the blade spar and root interface using our NASTRAN finite element software.
Sub-component test rig

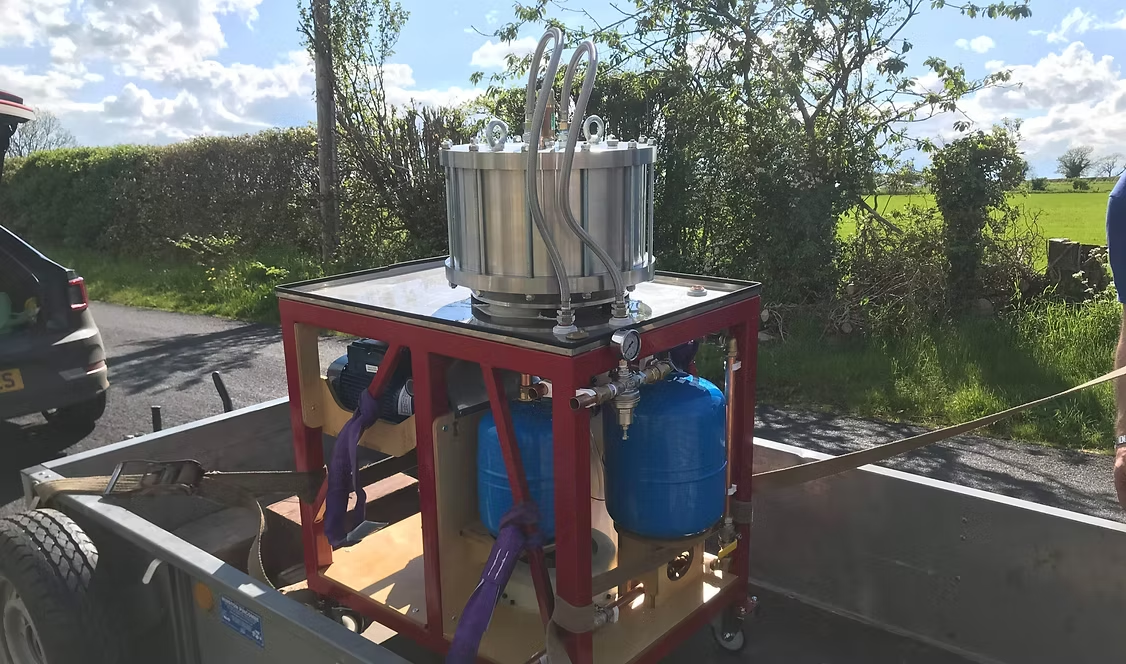
Working for the award-winning RheEnergise Ltd, we designed and manufactured a rig intended to evaluate the performance of sub-components destined for a novel energy storage system. The rig incorporates tightly toleranced machined and bolted assemblies, cost-effective welded frames, several safety features and numerous mechanical components such as bearings, couplings, motor and chain drive.
Composite materials R&D programme
Our ongoing composite materials R&D project aims to address the effects of seawater immersion on the performance of glass / epoxy laminates. Although much generic information is already available on this subject, the effects of seawater immersion tend to be highly resin system-specific with resins sold for the same purpose performing very differently. For this reason, we’re manufacturing and testing glass fibre panels using ten epoxy resin systems widely used in the marine industry; very interesting to see how each system compares against the others.
Although Orthotropic is a small company, we take a very serious approach to our manufacturing and test activities, as the quality of our efforts here underpins the reliability of our results: Full control and traceability of materials, processes and critical measurements can be taken for granted throughout.
We believe that this work will be of particular value to the marine renewables sector where durability of submerged composite structures is a really hot topic. Keep an eye on our news page for regular progress updates.
Covid face visors
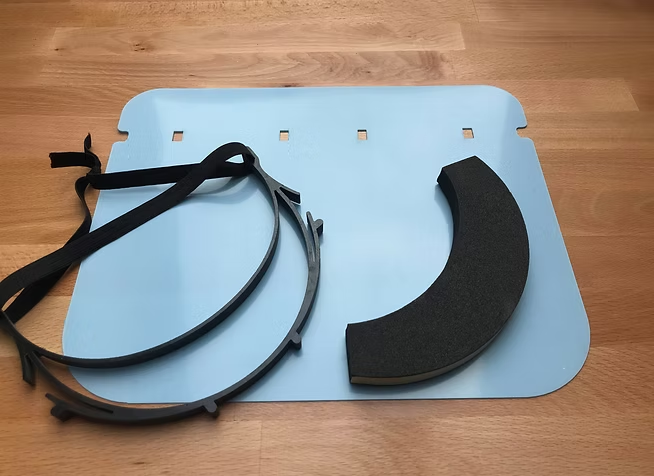
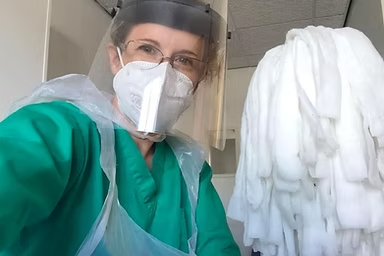
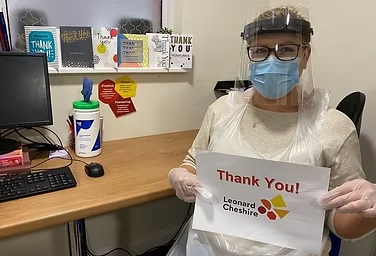
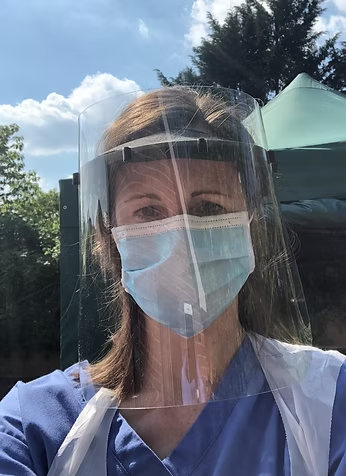
Not what we imagined we’d be doing at the start of the year but sometimes the world has other ideas! April 2020 saw our R&D workshop turned over to the manufacture of high-quality, reusable face visors that we supplied free of charge to hard-pressed care homes, NHS staff and schools. Adapting an existing open-source design for rapid manufacture and without charging for our time, we made and distributed 1000 visors in just over a month. Particular thanks to all who responded to our crowdfunding initiative (enabling the purchase of parts and materials) and those in our local community that lent a hand with manufacture and distribution.
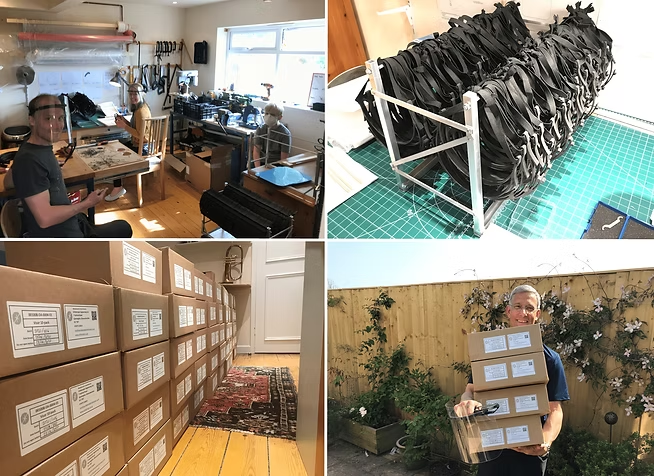