Composite laminate terminology
Like any other technical subject, the discipline of composites engineering is full of jargon. Of course, this is very much a mixed blessing: Although generally beneficial in speeding communication, any set of jargon has the potential to render discussions impenetrable to the uninitiated. Therefore, in this article, we attempt to explain in plain English a number of key terms relating to composite laminates.
Terms relating to fibres
The fibre is one of the two fundamental constituents of a fibre-reinforced plastic composite laminate. It is the fibre that provides the strength. A variety of fibres are available for incorporation in composite laminates, including, but not limited to glass, carbon, Kevlar, Dyneema, flax and hemp. Varying drastically in terms of cost, these fibres also possess a wide range of physical and mechanical properties, so the most suitable option will vary from application to application.
FRP is a generic term standing for ‘Fibre Reinforced Plastic’.
GFRP stands for ‘Glass Fibre Reinforced Plastic’
CFRP stands for ‘Carbon Fibre Reinforced Plastic’
Reinforcement is another term for fibre, and can also be used to mean fibres woven or stitched together in a form ready for combination with the matrix.
Sizing is a chemical treatment applied to the fibres in order to promote a strong fibre to matrix interface. The most appropriate sizing naturally varies depending on the type of matrix with which the fibre will be combined.
Tow is a term used to describe an untwisted bundle of continuous fibres or filaments. Predominantly used in association with carbon fibres, you’ll also hear plenty of talk of glass tows.
Yarn is a term used predominantly in conjunction with glass fibres. When used correctly, it implies a bundle of fibres that have been twisted together. The fibres may or may not be continuous.
‘K’ is a unit used to denote the number of fibres / filaments in a carbon tow, and means thousands. For example, a 12K tow will consist of 12000 fibres. Tows can vary between 1K and 50K or more.
Tex is a term used to denote the weight of a glass yarn or tow in grams / km. So, a 1km length of 1200 tex glass yarn would weigh 1200grams. Glass yarns are typically available between 300 and 9600 tex.
Terms relating to the matrix
The matrix is the second fundamental constituent of a fibre-reinforced plastic composite. It is the function of the matrix to bind the fibres together into a useful material, enabling their strength to be properly exploited, in compression as well as in tension. Polymer matrices may be broadly grouped into the thermosetting and thermoplastic categories. Whilst thermosetting matrices are generally more straightforward to process, thermoplastic matrices lend themselves more to recycling and may exhibit greater toughness.
Resin is a term often used interchangeably with ‘matrix’, although it should really be used to denote the liquid which, when combined with a suitable hardener or catalyst will polymerise or cross-link to form the matrix.
Thermosetting matrices typically comprise a liquid resin and hardener or catalyst that react, or ‘cure’ to form a network of long and covalently cross-linked polymer chains. Cure requires the application of temperature for a period of time (in some cases, room temperature is sufficient). Once cured, the form of a thermosetting matrix is set permanently. Thermosetting matrix options include polyesters, vinylesters, epoxies, phenolics and bismaleimides (BMI).
Thermoplastic matrices also comprise long polymer chains, but these are linked by weaker and non-permanent Van-der-Waals bonds. The Van-der Waals bonds may be broken by the application of heat, meaning that thermoplastic matrices may be liquified at high temperature and subsequently reformed. It’s for this reason that some thermoplastic matrices are supplied in solid form, although these typically require the application of significant temperature and pressure during moulding. Other options can be supplied as liquid resins that will polymerise on addition of a catalyst. Examples of thermoplastic matrices include PEEK and acrylics.
Exotherm is a phenomenon with which manufacturers of composite mouldings must cope. During cure, all thermosetting resins release heat, which will either be absorbed by the material, lost to the environment or a combination of both. As the rate of reaction is strongly temperature dependent (higher temperature = faster reaction), it’s easy to see how the temperature of a laminate may run away during cure. In the worst cases, this can result in fire. Runaway exotherm is particularly a concern when processing thick laminates as the achievement of adequate heat dissipation is naturally more of a challenge. Resins must be selected carefully to ensure that the reactivity will allow for a quick enough cure whilst avoiding an unacceptable level of exotherm.
Glass transition temperature (Tg) is one of the most important properties of a cured matrix, and is defined as the temperature at which the matrix will begin to soften and rapidly lose its mechanical properties. The combination of matrix and curing regime must be selected to ensure that the Tg will always be higher by a safe margin than the maximum operating temperature. Verification of Tg is a widely used check to ensure that a laminate has been properly cured.
Terms relating to reinforcement architecture
Fibre reinforcements are available in a wide array of architectures, as explained below. Layers, or plies of reinforcement are combined with the addition of a suitable resin to create laminates. Reinforcement weights are generally quoted in gsm (grams per square metre).
Non-Crimp Fabrics (NCFs) are a broad range of reinforcements constructed to avoid ‘crimp’ in the fibres. Crimp is a phenomenon experienced in woven fabrics where tows or yarns must pass over and under each other; as such, it has the effect of introducing weakness to a laminate, particularly in terms of its fatigue performance. Therefore, when we’re designing a part for high mechanical performance, we would typically want to use non-crimp reinforcements. The reinforcing fibres are normally held together by stitching (as opposed to weaving) and may run in a single, or multiple directions. NCFs are normally stored on rolls.
Unidirectional reinforcements (also UD / Unis) are those where all the fibres are arranged in the same orientation. This maximises the strength and stiffness of the reinforcement parallel to a single axis (the fibre direction). Of course, the reinforcement provides negligible strength and stiffness normal to the fibre direction. Such reinforcements are particularly useful where the stresses in a component are known to act along a single axis. Of course, unidirectional reinforcements may be combined in a laminate in multiple orientations in order to offer tailored properties.
Multiaxial reinforcements (typically NCFs) contain reinforcing fibres in more than one orientation. Multiaxial reinforcements may normally be classified as biaxial, triaxial or quadriaxial.
Biaxial (Biax) reinforcements (typically NCFs) contain fibres running in two directions. The most common combinations are at 0° and 90° to the roll direction and +45° and -45° to the roll direction (bias). Particularly in the case of 0° / 90° reinforcements, it is not a given that the fibres will be split evenly between the two orientations. Whilst such reinforcements don’t offer optimal strength or stiffness in a single direction, they make for very efficient manufacture of laminates where the stresses are known to be aligned in two key orientations. Biaxial reinforcements are also reasonably easy to ‘drape’ over or into a mould during manufacture.
Triaxial (Triax) reinforcements (typically NCFs) contain fibres running in three directions. The most common configuration consists of fibres oriented at 0°, +45° and -45° to the roll direction. The fibres may or may not be split evenly between the three directions. Triaxial reinforcements are particularly useful in elements of beam structures subject to combined axial and shear loading, however they do not drape easily over moulds exhibiting compound curvature.
Quadriaxial (Quad) reinforcements contain fibres running in four directions, normally 0°, +45°, 90° and -45° to the roll direction. If the fibres are split evenly between the four directions (which is not always the case), then the resulting laminate may be termed ‘Quasi-isotropic’ (QI), which is to say that its elastic and strength properties are substantially the same irrespective of orientation. This is about the closest that a composite laminate can get to sheet metal in its response to load, and whilst it is relatively ‘safe’ (no weak directions) it is not normally a particularly efficient use of material. However, there are applications such as lugs where QI laminates can be the most appropriate. It’s important to note that quad fabrics are unsuitable for draping over or into moulds exhibiting compound curvature.
Woven fabric reinforcements are a useful alternative to NCFs in many situations. Whilst NCFs exhibit superior mechanical performance, woven reinforcements tend to improve the damage resistance of a laminate due to the interwoven nature of the fibres. It’s also the case that in certain circumstances woven fabric reinforcements are easier to handle and process than NCFs. In particular, woven fabrics tend to drape much more easily in regions of compound curvature so are more suitable (at least in terms of manufacturing) for detailed and fiddly mouldings. The fibres in woven fabrics are normally classified in terms of ‘warp’ and ‘weft’.
Warp fibres are the long fibres running in the roll direction.
Weft fibres are those running across the roll of fabric. It’s not uncommon for the fabric to exhibit slightly lower strength in the weft direction, when compared with the warp.
Plain weave is the simplest type of weave imaginable. The weft fibres are woven through the warp in a ‘1 over, 1 under’ manner. The resulting fabric is fairly stiff to handle and highly crimped, therefore not often used.
2×2 Twill weave fabrics are often used in preference to plain weave. Their ‘2 over, 2 under’ weave pattern results in a lower level of crimp and more supple fabric than the plain weave. ‘2×2 twill’ is therefore often the default option when specifying a woven fabric.
Satin weave fabrics are woven in a ‘x over, 1 under’ pattern, where x is typically 3 or 4. The greater the value of x, the lower will be the level of crimp in the fabric, but the lower its stability.
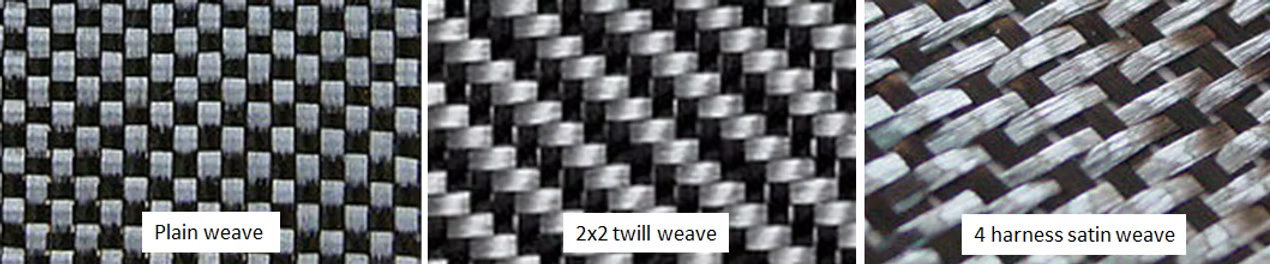
Chop(ped) strand reinforcements are short lengths of tow (normally glass) designed to provide a convenient and easily mouldable reinforcement suitable for gun application. The tows are typically chopped to 5-20mm in length and randomly oriented. Mechanical performance tends to be relatively poor, limiting the use of chopped strand reinforcements to non-structural or semi-structural applications.
Chop(ped) strand mat is similar in its characteristics and use to the chopped strand reinforcement mentioned above, the differences being that the fibres in chopped strand mat tend to be a little longer (~50mm) and that they are bound together as a mat for hand application.
Terms relating to laminates
A Sublaminate is a group of plies that is repeated several times through the laminate.
The Core is a low-density material (often foam sheet or honeycomb) that may be incorporated at or near the middle of a laminate to create greater elastic stability under conditions of shear and / or compressive loading for a relatively small mass penalty.
Sandwich panel is a term commonly used to denote a laminate containing a core.
Volume fraction (Vf) is the proportion of the total laminate volume occupied by the fibres. It is normally expressed in %. Composite laminates are commonly manufactured with volume fractions in the range of 20-60%. Toward the lower end of this range, we find low cost, low performance mouldings with chopped strand reinforcement, whilst the top end is inhabited by high-performance aerospace materials.
Resin weight is the proportion of the total material mass attributable to the resin. It follows for a void-free laminate that the resin weight may be calculated from the volume fraction and vice-versa, as long as the matrix and fibre densities are known.
Voids are unwanted manufacturing defects that often occur due to the inadvertent inclusion of air between plies in a laminate. In most applications it is impractical to completely eliminate voids so it’s important that the design is tolerant of their presence within certain limits, and that adequate quality measures are put in place to ensure that those limits are not exceeded in production.
Porosity is a collection of small voids.
Void content is the total volume of voids in a laminate expressed as a percentage of its total volume.
Fibre direction refers to the direction parallel to the fibres in any given ply.
Transverse generally refers to the direction in the plane of the ply that is normal to the fibre direction.
Through-thickness refers to the direction normal to both the fibre and transverse directions. (The name is a bit of a giveaway!)
The term ‘interlaminar’ refers to any effect occurring between adjacent plies. Examples include interlaminar shear stress and interlaminar cracks.