Fibre types and fibre selection
When specifying a composite part, one of the first questions facing the designer is that of fibre selection – the choice of fibre is a fundamental driver of laminate performance and cost, so picking the right option is of great importance! Fortunately, there are many types to choose from, offering a wide range of physical and mechanical properties and ranging from low cost to highly exotic. Of course, the sheer number of options on offer can be a little daunting, so in this article we explore the various types of fibre, their properties, typical applications, and pros and cons.
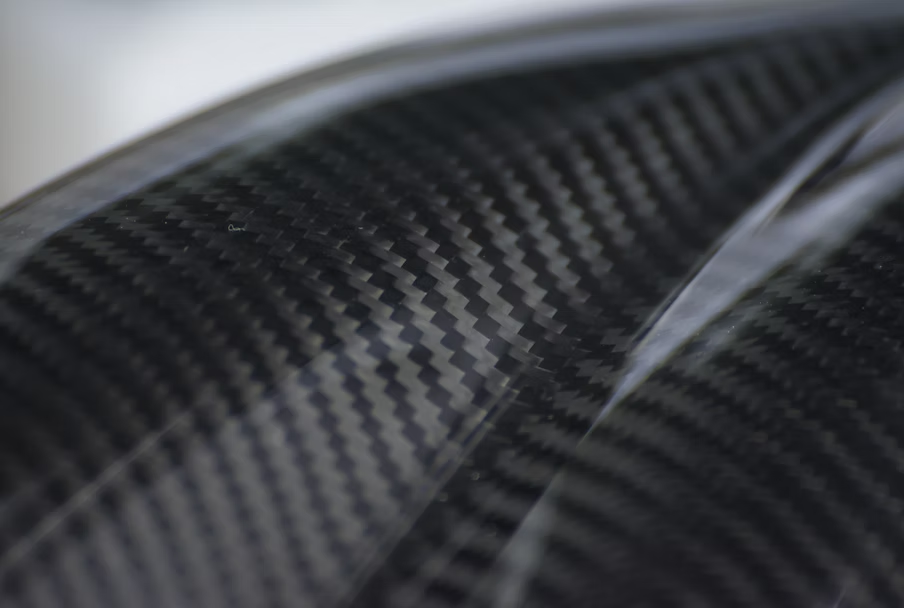
Carbon Fibres Say ‘composites’ and many people will think automatically of carbon fibre! Carbon fibres find their way into many high-end applications – deservedly so. They offer outstanding strength to weight and stiffness to weight ratios, making them the material of choice for numerous high-performance aerospace and motorsport applications. Further benefits of carbon fibres are exceptional fatigue performance and excellent resistance to harsh environments. They also exhibit a near-zero coefficient of thermal expansion (CTE) in the fibre direction – an advantage in some applications but an issue in others! The density of carbon fibres is in the range of 1700-1900kg/m^3, with most examples sitting quite close to 1800kg/m^3.
Carbon fibres consist of planes of graphene oriented parallel to the fibre direction. They are manufactured from either PolyAcryloNitrile (PAN) or mesophase pitch precursors.
PAN fibres are formed by drawing and stretching the precursor into fibres, thereby aligning their molecules. The fibres are then subjected to high temperatures, firstly in the presence of oxygen, then in its absence, causing strong cross-links to form between their molecules. In the case of pitch fibres, naturally-occurring pitch is heated above 350°C to cause condensation reactions that result in large, flat, mesophase pitch molecules aligned parallel to one another. The resulting viscous liquid is then extruded to form yarns which are oxidised, then thermally converted into a graphitic fibre at approximately 2000°C. In both cases, a chemical ‘sizing’ is applied to the fibres to promote adhesion in due course to the matrix component of the laminate.
Carbon fibres are available from several manufacturers in a wide variety of grades, each offering a different balance of strength, stiffness and, of course, cost. Typically, each product will correspond to one of three groups, High Strength (HS), Intermediate Modulus (IM) and High Modulus (HM).
- HS fibres are usually specified for ‘general purpose’ applications, offering high tensile strength, good stiffness and good handling robustness.
- IM fibres offer both higher tensile strength and stiffness (at higher cost) than HS fibres, so find application where particularly high performance is required.
- HM fibres offer exceptionally high stiffness, albeit with a similar tensile strength to HS fibres. Their use tends to be limited to those applications where the high stiffness is of paramount importance, as the cost of these fibres is high. Furthermore, their high stiffness renders them particularly susceptible to damage during processing and handling.
Despite their many advantages, there are of course several reasons why carbon fibres might not be the right choice for the job. The most obvious of these is cost: Where low weight or slenderness of structure aren’t absolute drivers, the use of carbon fibres can be difficult to justify. From an environmental standpoint, it’s also an inescapable reality that the manufacture of carbon fibres is an extremely energy-intensive process. Of course, in some cases, such as aviation, the through-life savings in fuel resulting from a lower-weight structure will more than compensate for the emissions embodied in the material itself. On a more practical level, carbon fibres are not transparent, so internal laminate defects cannot be detected by visual inspection alone.
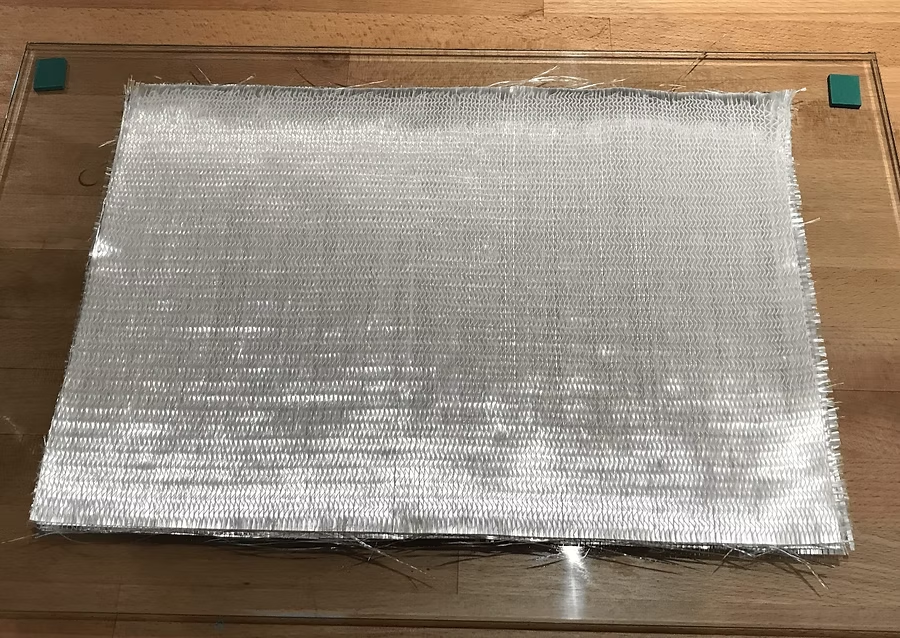
Glass Fibres – Where high specific strength and/or stiffness aren’t the be-all and end-all, glass fibres offer a very cost-effective and less energy-intensive alternative to carbon. Often selected for marine, renewable energy and industrial applications, they exhibit good strength, fatigue performance and stiffness for their weight and offer a coefficient of thermal expansion close to that of steel. In composite structures that must interface with steel fabrications, this particular characteristic can be advantageous in the avoidance of thermally-induced stresses. Furthermore, glass fibres are non-conducting, meaning that the incorporation of metallic fittings does not confer a risk of galvanic corrosion. The transparency of glass fibres can also be of benefit in cost-sensitive applications, as it permits the detection by simple visual inspection of certain laminate flaws. At 2500-2600kg/m^3, the density of glass fibres is higher than that of carbon, but still only a third that of steel.
Glass fibres are generally silica-based, with the addition of various oxides (aluminium, boron, calcium, iron, sodium) to tailor the properties. The raw ingredients are melted together at high temperature in a reservoir, before flowing under the action of gravity through perforated bushings and solidifying into fibres as they cool. As with carbon fibres, a chemical sizing is applied to the fibres at an early stage, in part to protect the fibres from damage but also to promote adhesion to the matrix when the fibres are subsequently incorporated in a laminate.
The most significant grades of glass fibre are E-glass and S-glass:
- E-glass is the low-cost ‘default’ fibre most widely used in the industry for several decades. Whilst suitable for low-budget processes and applications, it can nonetheless still be used to create relatively high-performing, cost-effective structures.
- S-glass is slightly stiffer and significantly stronger than E-glass. It also tends to be considerably more expensive. As such, it only finds use in very specific applications.
Increasingly of interest is E-CR glass. This is slightly stiffer and stronger than a standard E-glass but is claimed to be significantly more durable in aggressive environments, so is often specified for particularly demanding applications such as wind and tidal energy blades.
It’s important to note that the strength of glass fibres can be adversely affected by exposure to certain environments (for example marine), sometimes necessitating the use of non-trivial knockdown factors in the design process. Fortunately, this effect tends not to be a deal-breaker and can also be mitigated to an extent by careful selection of the matrix.
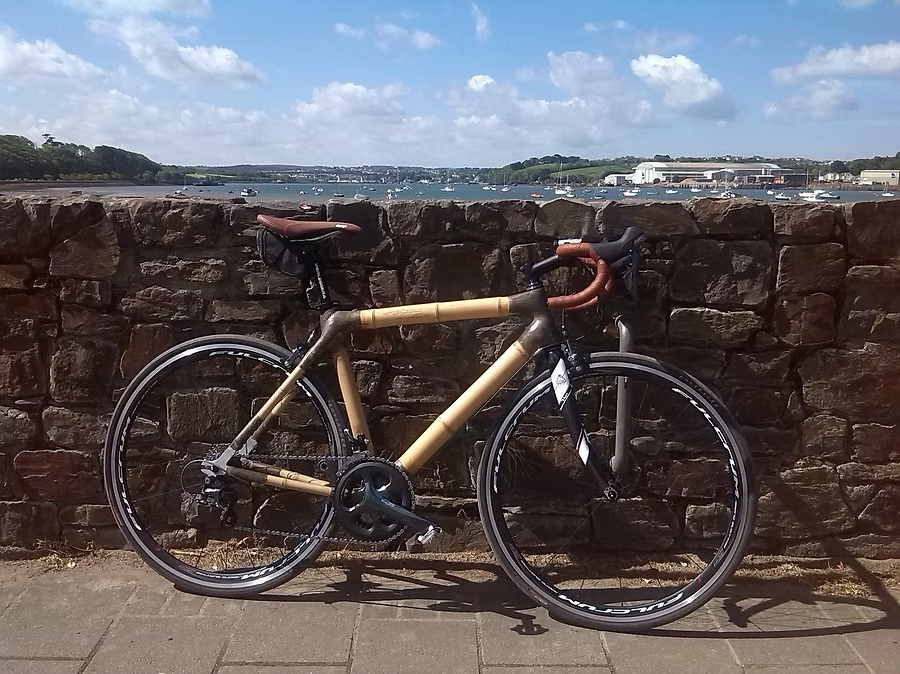
Natural fibres are becoming of increasing interest in recent years as they offer a more environmentally responsible manufacturing route than other options. Offering the most attractive mechanical properties in this category, the most commonly used natural fibre is flax, however hemp and jute fibres have also been used for various semi-structural and even structural applications. Natural fibres offer light weight (the density of flax fibres is approximately 1450kg/m^3), but relatively low strength in comparison to other fibre types.
One interesting application where this blend of properties appears to perform well is that of car bodywork. Another is in the construction of home-build bicycles, where bamboo frame members are successfully joined using hemp fibre and epoxy resins.
Of course, the attraction of biodegradability carries with it the perceived disadvantage of limited environmental resistance, so natural fibre composites tend not to find use in permanently immersed applications.
Aramid, or aromatic polyamides such as Kevlar are a class of fibres suited to particularly niche applications, their main selling point being a combination of light weight, high strength and high strain to failure. This makes them ideal for ballistics and penetration protection, as they are capable of absorbing very high levels of energy before failure. At 1440kg/m^3, the density of aramid fibres is very similar to that of flax.
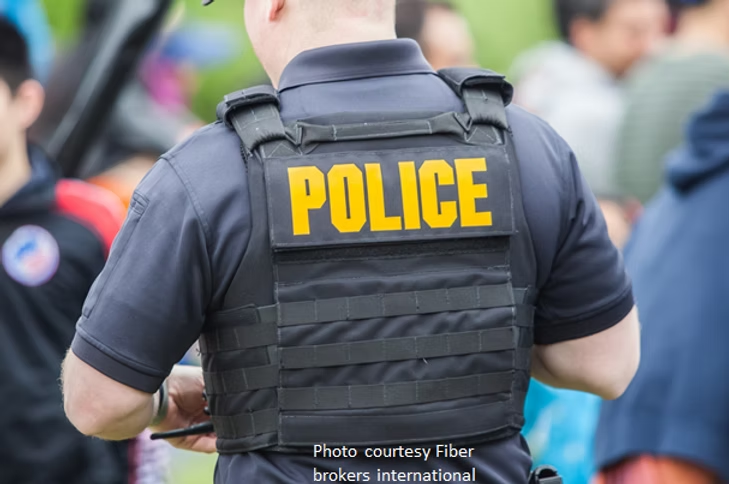
Mechanical properties
It’s interesting to directly compare the mechanical traits of the various fibres in terms of tensile strength and modulus (stiffness): We can see how the ‘high-strength, high-stiffness’ region of the chart is occupied entirely by the various types of carbon fibres, with the mechanical performance of glass and particularly flax fibres appearing very modest in comparison.
Of course, in many applications, the mass of the structure is also important, so ‘specific’ quantities – strength / density and stiffness / density become more relevant as selection parameters. Furthermore, the fibres are normally accompanied by an approximately equal volume of resin (sometimes more, sometimes less!), the added mass of which must be taken into account in any real-world comparison.
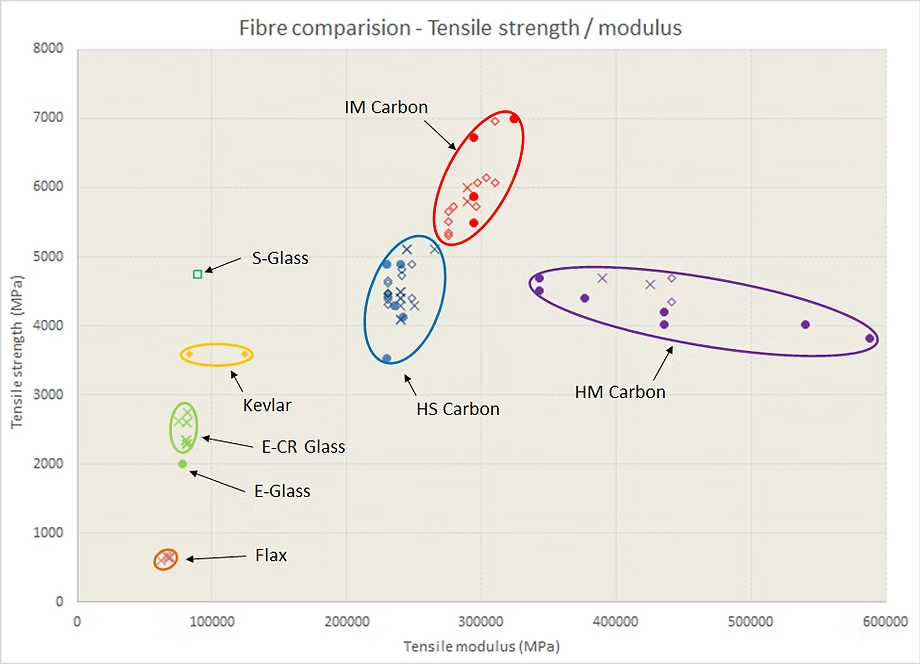
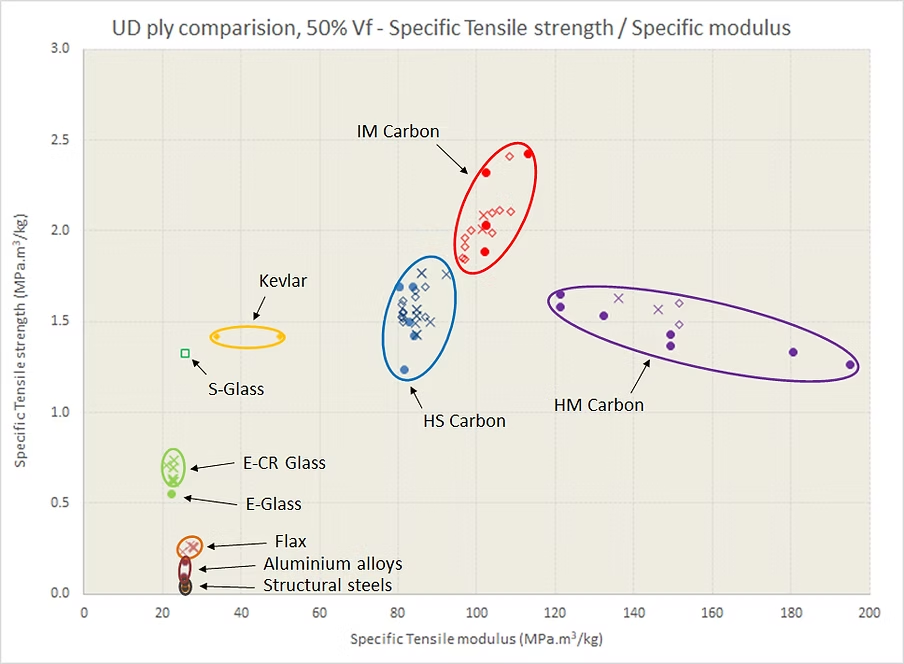
The second chart therefore shows fibre-direction specific strength plotted against fibre-direction specific stiffness for typical unidirectional plies at 50% fibre volume fraction. Under this set of considerations, the performance of carbon fibres remains exceptionally good. More interesting, however, is the relative improvement in performance of the lightweight flax ply, which shows a higher specific stiffness than glass. The specific strength of Kevlar plies is also high – on a par with the HS carbon plies. However, the lower specific modulus of the Kevlar means that a given mass has the capacity to absorb significantly more energy before rupture than the equivalent quantity of carbon.
It’s interesting to see that a unidirectional ply of any of the composite materials considered here compares favourably in terms of specific strength against both aluminium alloys and particularly structural steels. Of course, that’s not the end of the story: Real laminates almost always contain fibres running in more than one direction, which eats into their apparent advantage over metals: Fibres running across any given loading direction do not meaningfully contribute to the strength in that sense. It’s also necessary to consider that the compressive strength of a composite ply is normally considerably lower than its tensile strength and that the compression strength in particular can be sensitive to impact damage. When optimising for compression performance, elastic stability must be considered as well as strength. In such cases, the additional bulk of lighter materials will improve their relative buckling strength.
It would be interesting to create plots showing performance normalised against materials cost, but their validity would be hard to guarantee for long as the price of raw materials is rather volatile. In any case, where capital expenditure is the driver, glass fibre and particularly steel structures would be expected to perform far more strongly.
Of course, fibres aren’t much use on their own: Other than in very specific applications, a matrix is also required to provide stability, protection and load transfer capability. This second key constituent of composite materials will be discussed in a future article.